Firmen im Artikel
Die Multi-Jet-Fusion-(MJF)-Technologie und die innovativen 3D-Druckanlagen von HP setzen Meilensteine in der additiven Fertigung. Waren die gedruckten Teile früher oft nur als Prototypen oder Anschauungsobjekt geeignet, können Anwender dieser Technik heute auf sehr effizienten Anlagen robuste Bauteile schnell und kostengünstig herstellen. Externe Bauräume und Kühleinheiten ermöglichen einen 3D-Druck auf industriellem Niveau, während innovative Softwarelösungen Arbeitsvorbereitung und Fertigungssteuerung unterstützen.
Von Thomas Preuß, freier Journalist in Königswinter
Inhaltsverzeichnis
1. 3D-Druck im Multi-Jet-Fusion: Perfekte Oberflächen mit feinen Details
2. Dreimal so schnell wie das Lasersintern
3. Wachsende Materialpalette sorgt für steigende Vielfalt
4. Zwei Drucker-Familien für unterschiedliche Anforderungen
5. HP-Software hilft, den Bauraum optimal zu nutzen
6. Produktionszeiten drastisch verkürzen – bei höherer Flexibilität
7. Minimale Lager- und Transportkosten, effiziente Materialnutzung
Die Anforderungen des fertigungsgerechten Konstruierens haben der Kreativität der Entwickler und Konstrukteure im Maschinen- und Anlagenbau in der Vergangenheit oft Grenzen gesetzt. Auch eine kundenindividuelle On-Demand-Produktion war nur in begrenzter Form wirtschaftlich umsetzbar. Der 3D-Druck beendet heute diese Restriktionen in Konstruktion und Fertigung. Die sogenannte additive Fertigung eröffnet eine Welt voller neuer Möglichkeiten zur Produktion von Komponenten für Maschinen und Produktionsanlagen – sowohl bezüglich der Original- als auch der Ersatzteile. Der Einsatz von Multi-Jet-Fusion (MJF) von HP bietet dabei – im Vergleich zu anderen 3D-Druck-Technologien – bedeutsame Vorteile bezüglich Kosten, Geschwindigkeit und Qualität.
Entlang der Fertigungskette ermöglicht der Einsatz der HP-Multi-Jet-Fusion-Technologie
- Designfreiheit auch komplexer Geometrien
- Nachhaltigkeit durch den effizienten Einsatz leichter, langlebiger Werkstoffe
- einen optimierten Workflow durch ein Höchstmaß an Geschwindigkeit und Flexibilität sowie
- minimale Lager- und Transportkosten.
3D-Druck im Multi-Jet-Fusion: Perfekte Oberflächen mit feinen Details
Das Multi-Jet-Fusion-Verfahren nutzt einen Druckkopf, der über das gesamte Pulverbett reicht. Dieser sprüht zwei Flüssigkeiten in ein Bett aus Polyamid-Kunststoffpulver. Eine der Flüssigkeiten begünstigt die Wärmeaufnahme der Pulverkörner („Fusing Agent“), die andere bewirkt genau das Gegenteil („Detailing Agent“). Im Druckkopf sind starke Lampen installiert, die die Schicht aufheizen und die mit dem Fusing Agent besprühten Bereiche verschmelzen. Schließlich wird eine neue Pulverschicht auf das Druckbett aufgetragen, und der Vorgang wiederholt sich.
Die Multi-Jet-Fusion-Technologie erzeugt äußerst saubere Kanten, perfekte Oberflächen und sehr feine Details. Die erreichbare Auflösung in der XY-Ebene beträgt 1.200 dpi, die typische Schichtdicke 0,08 Millimeter. Darüber hinaus lassen sich mit diesem Verfahren auch Farbtinten versprühen, die farbige Ausdrucke ermöglichen. Ein weiterer Vorteil ist die sehr starke Bindung zwischen den Pulverkörnern und den Schichten. Dies sorgt für 100-prozentige Wasserdichtigkeit und verhindert ein anisotropes Verhalten, wie es viele 3D-Druckteile zeigen. Wie beispielsweise Holz sind anisotrope Teile in Schichtrichtung sehr belastbar, reißen aber gerne entlang der Schichtgrenzen und ertragen daher quer zur Schichtung geringere Kräfte.
Dreimal so schnell wie das Lasersintern
Das MJF-Verfahren bietet auch einen Vorteil in puncto Geschwindigkeit. Jede Sekunde trägt der Druckkopf 300 Millionen Tropfen Flüssigkeit mit einer Genauigkeit von 21 μm auf. So können bis zu drei Zentimeter pro Stunde aufgebaut werden, wohingegen Lasersintern lediglich einen Zentimeter pro Stunde erreicht. Die hohe Geschwindigkeit macht das Drucken in sehr kleinen Schichtdicken wirtschaftlich, während bei anderen Verfahren oft gröbere Schichten gewählt werden, um die Druckzeit nicht allzu lang werden zu lassen.
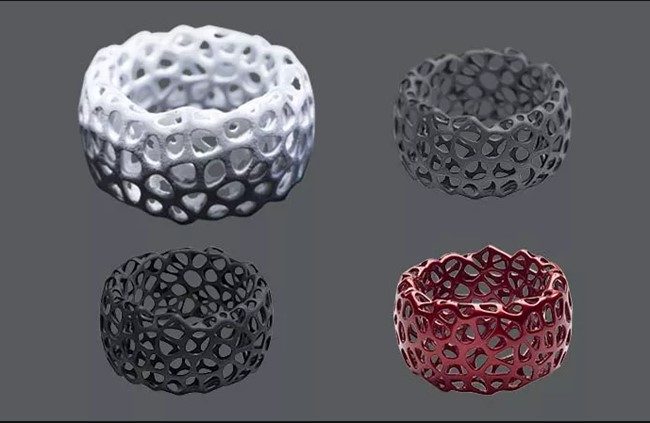
Darüber hinaus ist es vorteilhaft, dass das Pulverbett der Multi-Jet-Fusion-Drucker als Stütze für auskragende Bereiche der Modelle dient und keine Supportstrukturen notwendig sind, was beispielsweise bei FDM-Druckern der Fall ist. Damit entfällt das Entfernen der Stützstrukturen und das oft aufwendige Nachbearbeiten der Flächen, an denen die Stützstrukturen angeschlossen waren. Das übliche Post-Processing der mit HP-Druckern additiv gefertigten Bauteile besteht lediglich und je nach Bedarf aus dem Glasperlstrahlen, um die Oberfläche von letzten Anhaftungen zu reinigen, und dem Lackieren in der gewünschten Farbe.
Wachsende Materialpalette sorgt für steigende Vielfalt
Aktuell ist die Palette an Werkstoffen, die für den Druck mittels Multi-Jet-Fusion-Technologie verfügbar sind, noch überschaubar. Zahlreiche Partnerschaften zwischen HP und namhaften Materiallieferanten wie BASF, Evonik, Henkel oder auch Arkema lassen Vielfalt und Möglichkeiten aber stetig wachsen. Hier nur einige Beispiele:
- Mit HP 3D High Reusability PA11 hat HP ein Material im Angebot, das robust, aber auch verformbar ist. HP 3D PA12 ist steifer; noch mehr Festigkeit bietet HP 3D PA12 GB, das mit Glasperlen (Glass Beads, GB) angereichert ist. Alle drei Materialien lassen sich in den Druckern der Serien Jet Fusion 5200 und 4200 verarbeiten.
- Evonik hat das erste zertifizierte Partnermaterial für die Serie 4200 auf den Markt gebracht. Das PA12-basierte Vestosint 3D Z2773 ist ein günstiges thermoplastisches Material für die Herstellung von stark belastbaren Teilen.
- Mit dem Estone 3D TPU von Lubrizol steht für den HP Jet Fusion 4200 ein elastisches Material zur Verfügung.
- Neu ist das Ultrasint TPU01 von BASF, aus dem sich in der Serie 5200 elastische Funktionsteile erstellen lassen.
Zwei Drucker-Familien für unterschiedliche Anforderungen
HP bietet für den industriellen Einsatz zwei Familien mit unterschiedlicher Ausrichtung an. Die Jet-Fusion-4200-Serie ist im Grenzbereich zwischen Prototypen und Serienfertigung positioniert. Die praktisch baugleichen Geräte sind für 300 bis 699 beziehungsweise 700 bis 1000 Teile pro Woche ausgelegt und arbeiten mit einem Bauraum von 380 mm x 284 mm x 380 mm. Ein kompletter Druck dauert hier je nach Modus zwischen 11,5 und 16,5 Stunden. Das Gesamtsystem umfasst neben dem eigentlichen Drucker noch eine Processing-Station, in der die Bauteile und das überschüssige Pulver aus dem Bauraum entnommen werden und neues Pulver eingefüllt wird. Dazu ist der Bauraum in eine aus dem Drucker entnehmbare, fahrbare Building-Unit integriert. Die parallele Verwendung mehrerer Building-Units ermöglicht eine nahezu kontinuierliche Produktion ohne lange Stillstandszeiten.
Noch höheren Durchsatz erreichen die Drucker der Jet-Fusion-5200-Serie mit 300 bis 699 beziehungsweise 700 bis 1500 Bauteilen pro Woche. Ein kompletter Druck dauert hier ebenfalls je nach Gerät und Einstellung zwischen 9,5 und 16,5 Stunden. Auch bei diesen Geräten gehört die Processing-Unit zum Funktionsumfang. Hinzu kommen hier noch sogenannte Natural-Cooling-Units, in denen fertige Drucke außerhalb der Building-Unit auskühlen können.
HP-Software hilft, den Bauraum optimal zu nutzen
Um den vorhandenen Bauraum der Multi-Jet-Fusion-Drucker möglichst komplett auszunutzen, hat HP eine Software namens HP SmartStream 3D Build Manager entwickelt. Der Anwender lädt die zu druckenden Bauteile in einen virtuellen Bauraum, dreht und positioniert sie. Die Software prüft die Bauteilgeometrien und berechnet die optimale Positionierung. Fehler im Modell kann die Software auf Knopfdruck reparieren. Teile, die außerhalb des Bauraums liegen, werden farbig markiert. Dann lassen sie sich gezielt in den Bauraum verschieben oder über eine automatische Positionierung passend anordnen.
Eine effiziente Funktion für Dienstleister ist das sogenannte Caging, bei dem mehrere Teile in einem Gitterkäfig eingeschlossen und so gedruckt werden. So lassen sich Bauteile, die zu verschiedenen Aufträgen gehören, sehr einfach nach dem Drucken trennen.
Am Ende der Druckvorbereitung kann der Bediener die Druckdatei speichern oder an den angeschlossenen 3D-Drucker senden, um den 3D-Druck auszulösen. Der Druck selbst beziehungsweise die Drucke in mehreren Geräten lassen sich in der Software 3D Center überwachen und steuern. Zusätzlich bietet HP Schnittstellen zu externen Softwarepaketen wie Materialise Magics an.
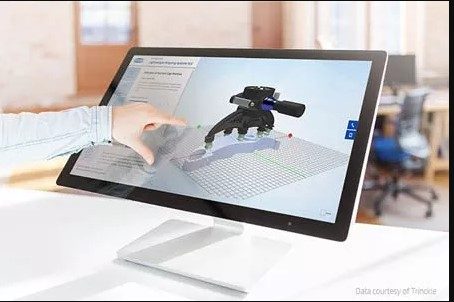
Mit dem 3D-Druck kann die Industrie heute einzigartige, nicht standardisierte Teile mit komplexer Geometrie problemlos fertigen, die mit herkömmlichen Produktionsverfahren nicht möglich wären. Durch Gitterstrukturen, optimierte Topologie sowie biometrische Strukturen ist es möglich, leichtere Teile mit verbesserten Eigenschaften zu konstruieren und herzustellen. Die 3D-Druckmaterialien sind darüber hinaus leichter als Stahl oder sogar Aluminium. Sie werden mit der Multi-Jet-Fusion-Technologie zu Komponenten verarbeitet, die in alle Richtungen nahezu die gleichen mechanischen Eigenschaften besitzen.
Auf diese Weise entstehen Bauteile, die trotz geringeren Gewichts nichts an Robustheit einbüßen. Der Anwender profitiert dabei von geringeren Kosten sowie von einem deutlich reduzierten CO2-Fußabdruck seiner Fertigung. Denn die für den 3D-Druck optimierten Konstruktionen tragen dazu bei, die Leistung der Maschinen und Produktionsanlagen zu verbessern. Sie sorgen für eine höhere Energieeffizienz, höheren Durchsatz, eine längere Lebensdauer und geringere Wartungskosten. Im Gegensatz zu herkömmlichen Produktionsmethoden verursachen Anpassungen oder komplexe Geometrien mit der MJF-Technologie keinen zusätzlichen Zeit- oder Kostenaufwand, auch nicht bei geringen Stückzahlen.
Produktionszeiten drastisch verkürzen – bei höherer Flexibilität
Da kundenspezifische Original- und Ersatzteile mit der MJF-Technologie im eigenen Haus gefertigt werden können, werden Ausfallzeiten von Maschinen und Produktionsanlagen sowie die damit verbundenen Kosten minimiert. Produktionszeiten lassen sich im Vergleich zu konventionellen Fertigungsmethoden von Wochen oder Tagen auf wenige Stunden reduzieren. Die bedarfsgerechte, parallele Vor-Ort-Produktion mehrerer neuer Teiledesigns steigert zudem die Flexibilität der Produktionsanlage deutlich. Die Anlagen lassen sich schnell und einfach auf ein neues Bauteil umrüsten.
Darüber hinaus profitieren gerade die Hersteller von Maschinen und Produktionsanlagen von der Produktionsgeschwindigkeit der MJF-Drucker, weil sie Anfragen von Kunden nach Originalersatzteilen jederzeit erfüllen und in der Regel innerhalb weniger Stunden liefern können. Auf Kundenseite werden so Maschinenkosten und Ausfallzeiten erheblich reduziert.
Minimale Lager- und Transportkosten, effiziente Materialnutzung
Der 3D-Druck kann dazu beitragen, die Lager- und Transportkosten im Vergleich zu traditionellen Produktionsmethoden zu reduzieren, da die exakt geforderten Stückzahlen kosteneffizient und schnell produziert werden – genau dann, wenn sie gebraucht werden. Die verkürzte Vorlaufzeit für die Ersatzteilbeschaffung führt zu minimierten Ausfallzeiten, womit die Kosten erheblich sinken können. Betreiber von Maschinen und Produktionsanlagen können zudem durch die Eigenproduktion von Originalersatzteilen ihre Reparatur- und Wartungskosten reduzieren.
Durch die konstruktive Anpassung an den 3D-Druck und die damit mögliche Funktionsintegration und Topologie-Optimierung kann zudem häufig Material eingespart werden, was zu weiteren Kostenreduzierungen führt. Verglichen mit anderen 3D-Drucktechnologien, lassen sich mit HP Multi Jet Fusion hochwertige Teile zu niedrigsten Kosten herstellen, auch dank der speziellen Verbrauchsmaterialien von HP (HP 3D High Reusability), die eine Wiederverwendbarkeit von bis zu 80 Prozent des überschüssigen Pulvers erlauben.