Pure Battery Technologies (PBT) hat gemeinsam mit der University of Queensland zwei neuartige Verfahren zur Produktion von Nickel-Mangan-Kobalt-Material entwickelt. In leistungsstarken EV-Batterien werden Nickel-Mangan-Kobalt-Oxide als Kathodenmaterial verwendet. Die neuen Verfahren sollen umweltfreundlich und kostengünstig sein und ermöglichen das Recycling alter E-Auto-Batterien.
Inhaltsverzeichnis
1. Neue Verfahren punkten durch Energieeinsparung
2. Nickel-Mangan-Kobalt aus allen Metallrohstoffen und -abfällen
3. Partnerschaften erwünscht
4. Vorteile der SAL- und CL-Verfahren in Zahlen
Lithium-Ionen-Akkus sind der meistverwendete Batterietyp in Elektroautos. Sie bestehen aus einer Anode, einer Kathode sowie einem Leitmedium. Die Kathode ist eine der teuersten und wichtigsten Komponenten in einer E-Auto (EV)-Batterie. Aufbau, Beschichtung und Qualität der Kathode bestimmen die Energiedichte der gesamten Batterie und damit die Leistungsfähigkeit des E-Autos. In leistungsstarken EV-Batterien werden Nickel-Mangan-Kobalt-Oxide (NMC) als Kathodenmaterial verwendet. Vor allem Nickel und Kobalt werden absehbar immer knapper und teurer. Zugleich steigt der Absatz an E-Autos (EV) und Fahrzeugen mit Hybridantrieb (PHEV) sprunghaft an. Für die Automobil- und Batteriewirtschaft ist die sichere Versorgung mit aktivem Vorläuferkathodenmaterial pCAM daher von entscheidender Bedeutung. Neue Quellen für die Versorgung mit Primärrohstoffen und zugleich das Recycling von Altmaterial werden dabei langfristig eine zentrale Rolle spielen.
Der für Batterien notwendige Metall-Mix Nickel-Mangan-Kobalt (NMC) kommt natürlich im Erdreich vor. In den herkömmlichen Raffinerieprozessen von Metallrohstoffen oder auch Metallabfällen, der sogenannten Black Mass, werden die drei Metalle Nickel, Mangan und Kobalt zunächst voneinander getrennt, dann von Unreinheiten befreit und schließlich erneut zu einer passenden Mischung zusammengeführt. Diese Verfahren mit vielen Schritten benötigen sehr große Mengen an Chemikalien, Wärme und Druck. Das alles erfordert Energie, erzeugt CO2 und verursacht hohe Kosten. An diesem Punkt setzen die patentierten Verfahren Selective Acid Leaching (SAL) und Combined Leaching (CL) an.
Neue Verfahren punkten durch Energieeinsparung
In zwei einfachen Schritten werden aus den vorhandenen Metallkonzentraten die Verunreinigungen gelöst und die Metalle gefiltert. Für diese chemischen Prozesse kommen sehr geringe Mengen von gängigen und vollkommen unschädlichen Oxidationsmitteln und Reduktionsmitteln zum Einsatz; diese werden in den Verfahren am Ende als harmlose Salze wiedergewonnen oder ausgeschwemmt. Aus dem Nickel- und Kobaltkonzentrat wird dann die passende Mischung für aktives Vorläuferkathodenmaterial pCAM produziert. Dieses kann kundenspezifisch angepasst werden.
Die bisherige Metalltrennung sowie Wiederzusammenführung entfallen. Wesentlich weniger Chemikalien, Wärme und Druck müssen eingesetzt werden. Energie, auch bei der Herstellung von Chemikalien, wird erheblich eingespart, wodurch sich der CO2-Ausstoß auf ein Minimum reduziert. Die eingesparte Energie sowie die entfallenen Prozessschritte reduzieren schließlich die Kosten und Dauer der Produktion des aktiven Vorläuferkathodenmaterials pCAM.
Nickel-Mangan-Kobalt aus allen Metallrohstoffen und -abfällen
Die von PBT entwickelten Prozesse sind sowohl für die Neuproduktion von Kathodenmaterial geeignet als auch für das Recycling der Black Mass, also dem aus alten Batterien zurückgewonnenen Kathodenabfall. Auch für die meisten künftigen Batterien, die auf der Lithium-Ionen-Technologie basieren, sind die Verfahren einsetzbar. Hier zählen auch die bei einigen Herstellern bereits für die nächste Fahrzeuggeneration vorgesehenen, leistungsstärkeren und preisgünstigeren Feststoffbatterien.
Partnerschaften erwünscht
Die beiden Verfahren SAL und CL von PBT fügen sich jeweils als fertiger Baustein in die bestehenden Wertschöpfungsketten ein. Deshalb plant PBT nicht nur den Aufbau umfangreicher, eigener Produktionskapazitäten. Vielmehr strebt das Unternehmen Partnerschaften mit seinen Kunden an. „Wir verhalten uns zu den einzelnen Industrien wie ein Zulieferer, an den eine wichtige Tätigkeit ausgelagert wird. PBT hat die bessere und effizientere Technologie. Die Kunden, ganz gleich, ob OEM, Kathoden- oder Batteriehersteller, können sich auf ihre Kernaufgaben konzentrieren“, sagt Thomas Fahrner, CEO der Pure Battery Technology Germany AG in Ettlingen.
„Wir werden mit unseren SAL- und CL-Prozessen die Erzeugung von Kathodenmaterial sowie das Recycling revolutionieren“, ergänzt Björn Zikarsky, CEO bei PBT-Holding. „Unsere Technologie ist erheblich effizienter als die bisher bekannten Prozesse. Wir haben damit eine Alleinstellung am Markt und wollen die bestehenden Prozesse ersetzen. Wir bieten das Verfahren Automobilherstellern, deren Zulieferern sowie der Batteriewirtschaft und der chemischen Industrie als fertigen Baustein für ihre Produktion von aktivem, nickelbasierten Kathodenmaterial an“, so Zikarsky. (eve)
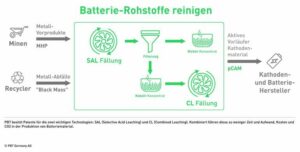
Vorteile der SAL- und CL-Verfahren in Zahlen
Energie-Einsparung:
Je nach Qualität des Vorprodukts 50% bis 80% weniger Energieverbrauch zur Herstellung von aktivem Vorläuferkathodenmaterial (pCAM). Diese Einsparungen entsprechen circa 4–6 kWh pro kg Nickel.
Niedrigere Prozesskosten:
Der vereinfachte Prozess senkt die Produktionskosten von pCAM erheblich. Kostenreduktion für das batteriefertige Vorläuferkathodenmaterial von US$ 2,50 pro kWh oder circa 5% der Gesamtprozesskosten einer Batteriezelle. Im Recycling eine Kostenreduktion von US$ 2,50 pro kWh oder circa 5% der Gesamtprozesskosten einer Batteriezelle.
Verringerter CO2-Ausstoß:
- 70% bis 85% weniger CO2-Ausstoß bei der Erzeugung von pCAM aus primären Rohstoffen.
- 55% bis 60% weniger CO2 bei der Verarbeitung von Black Mass der Metallabfälle zu pCAM.
- 960 kg weniger CO2-Ausstoß für die Umwandlung von Rohmaterial in batteriefähiges Vorläuferkathodenmaterial für eine 80 kWh-Batterie, die z. B. in einem SUV eingesetzt wird.
- 10% weniger zusätzlicher CO2-Ausstoß im Herstellungsprozess eines E-Autos.
- 30–80% der Batterieemissionen stammen aus der Rohstoffgewinnung.
- 20–30% weniger CO2-Emissionen in der gesamten Wertschöpfungskette.