Inhaltsverzeichnis
1. Roboter mit virtueller Spritzgießmaschine programmieren
2. Auch Unerfahrene können Heißkanalregler parametrieren
3. Mit OPC-UA-Standards wird die Branche zum Vorreiter
4. OPC UA macht immer mehr Maschinen kommunikationsfähig
5. Freigabe von Daten stößt noch auf Vorbehalte
6. Eine neutrale Datenplattform soll kommen
7. Das Werkzeug sendet Materialdaten
8. 30 % Produktivitätsgewinn durch künstliche Intelligenz
9. Künstliche Intelligenz sagt Materialverhalten voraus
10. Mit Simulation zur Recyclingfähigkeit
„Das müssen Sie sich anschauen, das ist ein Zukunftskonzept“, sagte Michael Wittmann kurz vor der Messe K2022. Der Chef des Kunststoffmaschinenbauers Wittmann Group meinte damit nicht einmal eine der neuartigen Maschinenanwendungen, sondern „Wittmann Holoverse“: Beim Rundgang auf dem Messestand konnte der Besucher eine „Hololens 2“ aufsetzen und sich mit ihr die Betriebs- und Prozessdaten an den laufenden Anlagen zeigen lassen – zum Beispiel den Füllstand und den aktuellen Durchsatz beim gravimetrischen Dosiergerät. Rezeptur und Materialverbräuche bekommt er in die Mixed-Reality-Brille eingeblendet. Der Bediener sieht alles auf einen Blick und behält die Hände frei.
Roboter mit virtueller Spritzgießmaschine programmieren
Sogar mit Sprachbefehlen lassen sich Spritzgießmaschine und Linearroboter steuern. 1500 solcher Kommandos haben die Experten ermittelt, die typisch sind für Spritzgießer – etwa „Maschine, starte Einspritzen“ oder „Roboter, schalte Vakuum ein“. Diese Spracheingabe stellte Wittmann schon 2021 vor, nun ergänzt durch virtuelle Elemente. Für die K2022 setzte Entwickler Stefan Dietrich noch eins obendrauf. Er erweiterte einen realen WX142-Roboter um eine in 3D animierte, virtuelle Spritzgießmaschine als Digital Twin. Zusammen simulieren sie eine funktionierende Fertigungszelle. Zum Benutzen braucht der Bediener nur eine MR-Brille.
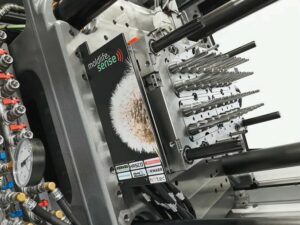
Bild: Arburg
Alles Spielerei? Es ist denkbar, dass die Bediener eines Tages so Anlagen konfektionieren und Fertigungsprozesse optimieren werden. Für den Datenaustausch zwischen Geräten und Hololens und zum Modellieren der Grafikobjekte kommt der Standard OPC UA zum Einsatz. UA steht für „Unified Architecture“.
Auch Unerfahrene können Heißkanalregler parametrieren
Noch ein Beispiel für Fortschritte durch Digitalisierung: Günther Heisskanaltechnik hat seine Temperatur-Regler der BlueMaster-Serien so weiterentwickelt, dass der User sie intuitiv über mobile Geräte bedienen und parametrieren kann.
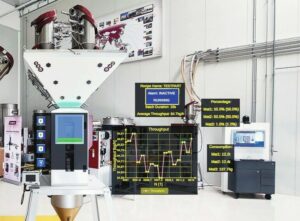
Bild: Wittmann-Gruppe
Auch Unerfahrenen soll das gelingen – bei kleinen Geräten über eine Smartphone-App, die mit Tutorials weiterhilft, und bei den größeren browserbasiert über ein Tablet. Diese größeren, für bis zu 24 Regelkreise ausgelegten „BlueMaster pro“-Heißkanalregler kommunizieren ebenfalls über OPC UA mit ihrer Spritzgießmaschine.
Mit OPC-UA-Standards wird die Branche zum Vorreiter
Um solche Standards mit der OPC-Foundation zu definieren (OPC = „Open Platform Communications“), sind die Verbände im Kunststoffmaschinenbau weit vorgeprescht. Die Liste der betreffenden Euromap-Schnittstellen wird immer länger. Damit lassen sich immer mehr Maschinen und Peripheriegeräte digital vernetzen und lernen, miteinander zu kommunizieren. Das macht die Branche zum Vorreiter für Industrie 4.0.
Als „besonders smarte“ Anlage präsentierte Arburg auf der Messe eine Fertigung für transparente Blutröhrchen. Die Spritzgießmaschine kommuniziert via OPC UA mit Werkzeug, Automation, Heißkanalregler und Materialtrockner. Die Komponenten stammen jeweils von verschiedenen Anbietern. Darin liegt der Charme der Spezifikationen: Sie überwinden die Sprachbarrieren von Marken. OPC UA ermöglicht bei der Blutröhrchen-Fertigung sogar ein Monitoring des gesamten Prozesses, inklusive Kamerabildern. Der Effekt sind Transparenz und höhere Effizienz.
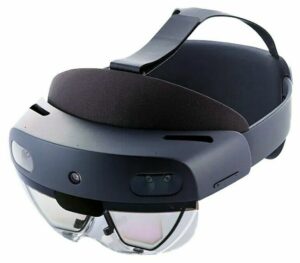
Bild: Wittmann-Gruppe
OPC UA macht immer mehr Maschinen kommunikationsfähig
Der VDMA bezeichnet OPC UA als die „Weltsprache der Produktion“ und will „die Lücken schließen“ in der Kunststoffverarbeitung. Dem Fachverband Kunststoff- und Gummimaschinen im VDMA ist das Thema so wichtig, dass er noch auf der Messe ein Interview mit Geschäftsführer Thorsten Kühmann publizierte und darin seine Positionen darlegte (s. unten). Der unmittelbare Nutzen von OPC UA seien besser gesteuerte Prozesse, sagte Kühmann. „Der viel größere Nutzen liegt aber in der Möglichkeit, künftig digitale Serviceleistungen anzubieten. Dazu braucht man zwingend viele Daten aus dem Feld.“
Freigabe von Daten stößt noch auf Vorbehalte
Doch hier gibt es auch Bedenken. Besonders Verarbeiter fürchten, ihre Daten könnten in falsche Hände geraten. Das bekommen unter anderem die Spritzgießmaschinenbauer zu spüren. Engel etwa ist dabei, sein Kundenportal zum „Produktionsportal“ auszubauen und öffnet es für andere Marken. Das Portal biete umfangreiche Möglichkeiten zur Prozessanalyse. Das integrierte Assistenzsystem „iQ process observer“ etwa könne hunderte Prozessparameter analysieren und mit vorigen Zyklen abgleichen. Es nutzt dafür künstliche Intelligenz (KI). Der Effekt sind Produktivitätssteigerungen.
Doch die Kunden zögern. Engel bietet darum Basis- und Premium-Zugänge an. „Wir wollen unsere Kunden nicht überfordern und dort abholen, wo sie mit ihrem Digitalisierungsgrad und ihrer Philosophie stehen“, sagte CTO Dr. Gerhard Dimmler auf der Messe.
Eine neutrale Datenplattform soll kommen
Der VDMA kann die Sorge der Kunststoffverarbeiter nachvollziehen. „Im Moment sind wir soweit, dass wir sehr viele Daten sammeln können. Als nächstes brauchen wir eine vertrauenswürdige Plattform, auf die diese Daten geliefert werden können“, erklärt Thorsten Kühmann im Interview (s. unten). Der VDMA beteilige sich daher an dem von der Bundesregierung lancierten Förderprojekt Manufacturing-X, das genau dies zum Ziel hat. „Sonst laufen wir Gefahr, dass große Datenanbieter das Ganze an sich ziehn. Das will aber keiner in der Industrie“, so Kühmann.
Big Data sind die Treiber der Digitalisierung. Sie schließen die Maschinendaten ein, gehen aber noch weit über sie hinaus. Visionäre dachten schon immer, aus der Datenfülle in der Industrie müsse sich mehr machen lassen. Jetzt ist es so weit. Die K2022 deutete erste Ansätze und Lösungen an. Die Akteure nutzen KI als Tool, um große digitale Datenmengen mit dem ihnen verfügbare Wissen zu durchforsten und auszuwerten.
Das Werkzeug sendet Materialdaten
SensXpert ist zum Beispiel aus der im Pumpenbau groß gewordenen Netzsch-Gruppe hervorgegangen. Das im Juli 2021 offiziell ausgegründete Unternehmen macht sich die 50-jährige Erfahrung der Gruppe in der Materialcharakterisierung zunutze. Es realisiert damit datengestützte Fertigungslösungen.
Das Spin-off geht mit In-Mold-Sensoren in die Kunststoffschmelze im Werkzeug und leitet dynamische Materialkennwerte wie Aushärtegrad, Fließfähigkeit, Phasenübergänge oder Schwindung aus den Signalen ab. „In Echtzeit erkennen wir Zustände und Schwankungen, die kein Temperatursensor erfassen kann“, erklärt Geschäftsführerin Cornelia Beyer. Damit werde es möglich, noch viel mehr aus den Prozessen zu holen, beispielsweise aus dem Spritzgießzyklus.
30 % Produktivitätsgewinn durch künstliche Intelligenz
Netzsch hat diesen Transfer selbst in die Hand genommen. Die offizielle Firmierung des Spin-offs als „Netzsch Process Intelligence GmbH“ ist Programm: SensXpert verspricht um bis zu 30 % höhere Produktionseffizienz durch seine lernenden Fertigungssysteme. Weitere Effekte seien bis zu 50 % weniger Ausschuss, bis zu 23 % weniger Energieverbrauch und stark reduzierte Stillstandszeiten. Dafür gebe es Referenzen von Pilotkunden wie ZF.
Die Basis bildet künstliche Intelligenz. Die KI wertet die Sensorik von Drittanbietern mit aus. Cornelia Beyer spricht von einer Plattform für ganzheitliche Datenaufbereitung: „Die intelligente Maschine und das intelligente Werkzeug müssen zusammenkommen. Wir teilen die Daten. Es ist ein Geben und Nehmen.“
Herzstück des Produkts „SensXpert“ bildet ein Edge Device. Im Rahmen einer „Equipment-as-a-Service“-Lösung wertet es die ermittelten Material-, Maschinen- und Prozessdaten in Echtzeit aus und steuert den Prozess. Über die Cloud werden die Lernmodelle mit gemessenen und experimentellen Materialwerten ständig trainiert und kontinuierlich präzisiert.
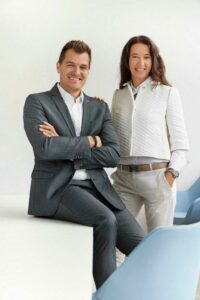
Bild: SensXpert
Künstliche Intelligenz sagt Materialverhalten voraus
Auch Altair berichtete über Fortschritte bei Material Data durch KI. Schon vor der Kunststoff-Leitmesse machte das Software-Haus auf seine digitale Expertise aufmerksam. Als „führend“ im Bereich Computational Science und Künstliche Intelligenz könne es digitale Twins für jede Phase des Produktlebenszyklus ermöglichen, bis hin zur Gesamtlösung. Altair spricht vom „One Total Twin“.
Material Data sind wichtig dafür. Vor zwei Jahren übernahm Altair die Materialdatenbank „Mbase“. Die so ins Unternehmen gelangten Materialkundler trainieren KI mit Werten aus Tests und der Datenbank. „Wir haben jetzt ein Modell, das selbst bei spärlichen Eingaben verlässliche Aussagen über Materialeigenschaften machen kann“, konstatiert Mirko Bromberger, Marketingleiter DACH.
Mit Simulation zur Recyclingfähigkeit
Diese Option beflügelt nicht nur Materialentwickler. Sie fließt auch in Altair-Tools ein. Was diese im Kunststoffbereich leisten können, zeigt Verpackungshersteller Alpla: Mithilfe der Simulation entwickelten Alpla-Ingenieure das Nachfüllsystem „Simple One“ der Kosmetikmarke Susanne Kaufmann: zu 100 % aus Rezyklat, sehr ästhetisch und voll recycelbar. Dafür wurde es ausgezeichnet.
Noch weitere KI-Lösungen gab es auf der K‘ zu entdecken, teils versteckt. Technotrans präsentierte auf dem Messestand live eine KI-basierte Prozessdatenüberwachung von Spritzgießmaschinen und Temperiergeräten. In der Fachzeitschrift „K-Profi“ 10/22 war zu lesen, wie der Thermomanagement-Spezialist dazu Daten über OPC UA gewann und mit Geschäftspartner Nexocraft eine KI trainierte. Das Start-up Aisemo stellte eine KI-Software vor, die sich plug&play und berührungslos zur Prozessüberwachung installieren lässt. Die nächste K‘ ist in drei Jahren. Auf ihr wird wohl einiges mehr in dieser Art zu sehen sein.
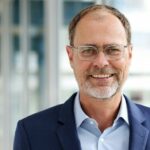
Bild: VDMA
„Alle Maschinen müssen dieselbe Sprache sprechen“
Auf der Kunststoff-Leitmesse K2022 positionierte sich der VDMA zu OPC UA im folgenden Interview mit Fachverbands-Geschäftsführer Thorsten Kühmann. Die Fragen sind hier teils verkürzt wiedergegeben.
Herr Kühmann, welche Rolle spielt OPC UA auf der Messe?
Hier auf der K beteiligen sich 40 Unternehmen aus acht Ländern an einem OPC UA-Demonstrationsprojekt. Sie haben an ihren jeweiligen Hallenstandorten insgesamt 85 Maschinen dafür ausgesucht. Jede dieser Maschinen ist neben einem OPC UA-Logo mit einem QR-Code versehen. Den kann der Besucher mit seinem Smartphone scannen. Er kommt dann auf die Internetplattform UMATI und kann dort Live-Daten der jeweiligen Maschine sehen.
Was nimmt der Bedeutung mit von dieser OPC UA-Demo?
Zur größeren Veranschaulichung haben wir im VDMA Dome ein großes Dashboard installiert. Der Besucher kann auf jede einzelne Maschinen zusteuern, um zu sehen, welche definierten Daten sie liefert. Das Wichtigste ist, dass alle Maschinen dieselbe Sprache sprechen, sie nutzen alle dasselbe System. Wir stellen fest, dass das Interesse der Besucher enorm groß ist. Es gibt sehr viele Nachfragen.
OPC UA treibt also die Digitalisierung in der Produktion voran?
Ja, und zwar in zweierlei Hinsicht. Der direkte Nutzen besteht in der sehr schnellen Schaffung von Transparenz. Man weiß, welche Daten es gibt und man kann sich aussuchen, welche Daten wichtig sind. Die Transparenz ermöglicht dann eine bessere Steuerung der Prozesse. Der viel größere Nutzen liegt aber in der Möglichkeit, künftig digitale Serviceleistungen anzubieten. Dazu braucht man zwingend viele Daten aus dem Feld. Die sind im Moment noch gar nicht verfügbar, weil die ganze Infrastruktur noch nicht vorhanden ist. Hier liegt aber das größte Potenzial. OPC UA ist sozusagen die Vorbereitung darauf.
Wie weit ist man in der Umsetzung bei Kunststoff- und Gummimaschinen?
In einigen Kernmaschinenbereichen sind wir schon recht weit gekommen, etwa beim Spritzgießen oder in der Extrusion. Jetzt geht es weiter, beispielsweise zum Partikelschäumen und natürlich auch in die Peripherie. Es werden also etwa Temperiergeräte und Heißkanalgeräte miteinbezogen oder die Flüssigsilikondosierung. Das ist die horizontale Ebene: Die Maschinen, die in einer Produktionshalle nebeneinander stehen, können miteinander kommunizieren. Ein weiterer Strang ist die vertikale Vernetzung zum MES-System, das die Daten einer Fabrik zentral verarbeitet.
Gibt es zur K etwas Neues?
Ab jetzt ist auch der Materialfluss einbezogen. Zur K wird die neue Schnittstelle für Material Supply System vorgestellt: die OPC 40086–1. Das ist ein sogenannter Release Candidate. Das bedeutet, er ist konzeptionell fertig, kann aber noch ergänzt und angepasst werden. Wir haben somit heute schon eine solide Grundlage für OPC UA im Bereich Kunststoff- und Gummimaschinen aufgebaut.
Was sind die nächsten Schritte?
Wir wollen die Lücken schließen. Wir haben noch Maschinen, die nicht eingebunden sind. Auch muss die Internationalisierung trotz guter Fortschritte weiter vorangetrieben werden. Denn das Ganze macht erst richtig Sinn, wenn möglichst viele Länder dabei sind. Erst dann kann man wirklich herstellerübergreifend kommunizieren. Im Moment sind wir soweit, dass wir sehr viele Daten sammeln können. Als nächstes brauchen wir eine vertrauenswürdige Plattform, auf die diese Daten geliefert werden können.
Schrecken nicht viele davor zurück, eigene Produktionsdaten außer Haus zu geben?
Gerade die Verarbeiter sind bei OPC UA-Anwendungen noch sehr zurückhaltend. Sie haben Sorge, dass nicht sorgsam mit ihren Daten umgegangen wird und schlimmstenfalls sogar ihre Wettbewerber Zugang zu ihren Daten bekommen. Ein Teil des Problems liegt darin, dass solche Datenplattformen bislang nur von einzelnen Firmen oder kleinen Konsortien angeboten werden. Denen vertrauen die Anwender offenbar nicht. Deswegen steuern wir gerade in eine ganz andere Richtung. Wir versuchen, eine vertrauenswürdige, neutrale Plattform zu etablieren und beteiligen uns als VDMA daher an dem von der Bundesregierung lancierten Förderprojekt Manufacturing-X, das genau dies zum Ziel hat.
Welche Vorteile könnte eine solche neutrale Datenplattform haben?
Wenn der Rahmen der Plattform gesetzt ist, wenn also Fragen der Governance, der Datensicherheit oder auch der Haftung geklärt sind, kann im Prinzip jeder diese Plattform unter diesen Bedingungen nutzen. Es ist wichtig, dass wir so eine Plattform etablieren, denn sonst laufen wir Gefahr, dass große Datenanbieter das Ganze an sich ziehen. Das will aber keiner in der Industrie, weder auf Kundenseite, noch auf Maschinenbauseite.
Inwieweit begünstigt dies das Projekt Kreislaufwirtschaft?
Zunächst einmal durch die schnelle Transparenz. Sie ermöglicht es, Maschinen und Prozesse mithilfe der erhobenen Daten besser steuern zu können. Das ist wichtig für die Kreislaufführung, weil man dadurch zum Beispiel die Energieeffizienz verbessern kann. Man kann genau erkennen, wo im gesamten System wieviel Energie verbraucht wird. Man bekommt also den Energiekreislauf damit besser in den Griff.
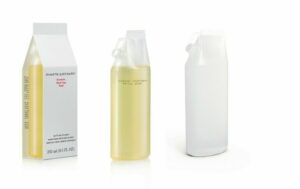
Bild: Altair
Und im Blick auf Rezyklate?
Beim Materialkreislauf geht es darum, beispielsweise in einem verarbeitenden Unternehmen, die Rezyklatverarbeitung zu verbessern. Die ist herausfordernder als bei Neuware, weil Rezyklate teilweise inhomogener sind. Mithilfe von OPC UA und dem damit verbundenen Informationsaustausch kann man die Verarbeitungsparameter der beteiligten Maschinen und Geräte genauer und gezielter aufeinander abstimmen. Das sind wichtige Beispiele für die optimierte Kreislaufführung.