Herr Horn, Ihr Unternehmen übernimmt auf Wunsch das komplette Werkzeug-Engineering. Können Sie uns an einem Beispiel beschreiben, wie eine solche Partnerschaft abläuft?
Ein schönes Beispiel dafür ist unsere Kooperation mit Midual, einem französischen Hersteller von sehr edlen und innovativen Motorrädern. Dort liefern wir Werkzeuge sowohl fürs Bearbeiten des Aluminium-Sandguss-Monocoques als auch einiger Motorkomponenten und Anbauteile. Grundsätzlich gibt es zwei Ausgangsszenarien, wenn wir eine Werkzeuglösung auslegen. Entweder kommt ein Kunde gezielt auf uns zu und fragt nach einer Lösung für ein Fertigungsproblem, oder der Kontakt entsteht, wenn unser Außendienst bei einem Besuch erfährt, dass der Kunde an der einen oder anderen Stelle mit seinen bisherigen Prozessen nicht glücklich ist. Oft kann unser Außendienst dann bereits eine bessere Alternative vorschlagen. Wenn´s komplexer wird, erarbeitet er – gegebenenfalls in Zusammenarbeit mit den Spezialisten bei uns im Haus – ein passendes Werkzeug, optimierte Prozessparameter oder eben eine alternative Prozessführung mit einem anderen Fertigungsverfahren.
Wo lagen bei Midual die besonderen Herausforderungen?
Ein Thema war das Planfräsen des zweiteiligen Motorgehäuses aus Aluminium. Weil diese Flächen zugleich als Dichtflächen dienen, muss diese Bearbeitung hohe Anforderungen an die Präzision, Ebenheit und Oberflächengüte erfüllen. Hier setzt der Kunde unser Frässystem DTM mit PKD-Schneiden ein, das zudem auch einige Sicht- und Dekorflächen zum Glänzen bringt. Fürs Stoßen von Steckverzahnungen, etwa im Schalthebel, kommt unser System Supermini Typ N105 zum Einsatz. Und auch viele Anbauteile fertigt Midual mit unseren Werkzeugen aus dem Vollen.
Können Sie bei solchen Projekten auf Standard-Werkzeuge zurückgreifen?
Eine Regel ist hier schwierig zu definieren. Es kommt immer auf das jeweilige Projekt an. Es ist möglich, dass wir alle Anforderungen mit Standardwerkzeugen erfüllen können. Genauso kann es aber sein, dass wir ausschließlich auf Sonderwerkzeuge setzen. Und auch jede Mischung ist denkbar.
Hängt das von der Losgröße ab?
Ja und nein. Bei der Großserienfertigung ist die Taktzeit ein großes Thema, und wenn wir hier durch Sonderlösungen oder eine alternative Prozessführung Vorteile beim Kunden erzielen können, dann rechnet sich das natürlich eher als in der Prototypen- oder Kleinserienfertigung. Durch die Auswahl des Substrats, der Beschichtung, des Werkzeughalters oder des Prozesses an sich können wir die Bearbeitung beeinflussen und so effizienter und wirtschaftlicher gestalten. Andererseits ist gerade Midual ein Beispiel, bei dem angepasste oder spezielle Werkzeuge auch in der Kleinserienfertigung einen wesentlichen Vorteil hinsichtlich Präzision, Oberflächengüte oder auch Bearbeitungszeit bringen können. In der Regel kommen für einfachere Bearbeitungen Standardwerkzeuge zum Einsatz und wenn die Anforderungen steigen, sei es hinsichtlich der Taktzeit, der Qualität oder der Standzeit der Werkzeuge, dann kommen zunehmend Sonderlösungen ins Spiel.
Horn ist bekannt für Hartmetall-Werkzeuge. Bei Midual kommen auch PKD-Tools zum Einsatz. Welche Rolle spielt dieser Schneidstoff in Ihrem Haus?
Es stimmt zwar, dass unser Ursprung bei den Hartmetall-Werkzeugen liegt. Unser Portfolio ist aber schon lange deutlich breiter. Wir bieten heute fast alle relevanten Schneidstoffe an. Bei poly- oder monokristallinem Diamant geht´s darum, extrem glatte bis hin zu hochglänzende Aluminiumoberflächen herzustellen. Genau das war bei Midual ein wichtiges Thema. Deshalb PKD als Schneidstoff. Wenn die Ansprüche an die Oberflächengüte steigen, steigen auch die Kosten, da dann PKD zum Einatz kommt. Deshalb legen wir Wert darauf, immer das Optimum aus Qualität und Wirtschaftlichkeit zu finden.
Stammen die PKD-Schneiden aus der eigenen Produktion?
Ja. Wir bieten PKD-Werkzeuge seit über 20 Jahren an. In dieser Zeit haben wir natürlich spezifische Anlagen und Prozesse installiert sowie die Mitarbeiter entsprechend geschult, die genau diesen Themenbereich beherrschen. Von der Halterfertigung bis zur Schneidkantenpräparation, der Laser-Bearbeitung und Auslieferung machen wir auch hier alles im Haus.
Stellt Horn – wie beim Hartmetall – auch die PKD-Substrate selbst her?
Ich würde sehr gerne sagen: Ja! Das würde unserer DNA entsprechen. Aber der Prozess ist sehr aufwändig und aufgrund seiner Energieintensität in Deutschland kaum wirtschaftlich machbar. Deshalb kaufen wir die Ronden zu, stimmen uns dabei aber eng mit den Lieferanten ab, um die Substrate an unsere Anforderungen anzupassen. Dadurch haben wir eine breite Auswahl an funktionierendem Schneidstoffmaterial.
Hochglanzfräsen, das bei Midual eine große Rolle spielt, ist normalerweise eine Domäne von MKD. Wie gelingt es, das auch mit PKD zu erfüllen?
MKD-Schneiden werden aus einem großen Diamantblock hergestellt. PKD besteht hingegen aus vielen kleinen Diamantstückchen, die von einem Bindemittel zusammengehalten werden. Über die Menge und die Größe dieser Diamantkörner sowie den verwendeten Binder lassen sich die Eigenschaften von PKD an die jeweiligen Anforderungen anpassen – etwa in Richtung Zähigkeit oder einer höheren Schneidkantenqualität. Über diese Stellschrauben lassen sich mit PKD durchaus auch hochglänzende Oberflächen erzeugen, die allerdings nicht die Qualität erreichen, die etwa bei technischen Spiegeln gefordert ist.
Die Trägerwerkzeuge stellen Sie aus Gewichtsgründen aus Aluminium her. Reicht deren Stabilität und Verschleißfestigkeit aus?
Beim Fräsen mit PKD-Werkzeugen arbeiten wir mit hohen Drehzahlen. Entsprechend dynamisch und perfekt ausgewuchtet müssen die Werkzeuge sein, um höchste Qualität zu liefern. Damit die Grundkörper trotz des weicheren Materials beispielsweise gegen herumfliegende Späne geschützt und verschleißfest sind, erhalten sie eine Schutzbeschichtung.
Handelt es sich dabei um ähnliche Beschichtungen wie bei den Schneiden?
Wenn man sich überlegt, was die Schutzschicht einer Hartmetallschneide im Einsatz aushalten muss, dann ist die Belastung eines Trägerwerkzeugs deutlich geringer. Insofern brauchen wir hier nicht die gleichen High-end-Beschichtungen.
Gibt es etwas, das Horn und Midual besonders verbindet?
Mit Midual verbindet uns sicher die Technikverliebtheit, das Streben nach innovativen Lösungen sowie der hohe Anspruch an die Qualität und das perfekte Ergebnis. Zudem streben wir beide danach, möglichst viele Prozessschritte im eigenen Haus zu erledigen und zu beherrschen. In diesem Sinne haben wir auch beim Glanzfräsen eine Lösung gefunden, die diesen Ansprüchen gerecht wird. Aber solche Ergebnisse lassen sich nicht im Vorbeigehen erzielen. Dazu müssen alle Prozesselemente ideal harmonieren.
Wie unterscheiden sich die Anforderungen ans Werkzeug beim Verbrennungsmotor im Vergleich zur E-Mobilität?
Die Anforderungen unterscheiden sich in zwei wesentlichen Aspekten: Zum einen haben wir in der Elektromobilität einen relativ hohen Anteil an Aluminiumteilen und sonstigen Leichtbaulösungen, die das hohe Gewicht der Batterien kompensieren können – allerdings sehen wir diesen Trend inzwischen auch vermehrt bei den klassischen Fahrzeugkonzepten, bei denen das ebenfalls zu einer höheren Effizienz führt. Der zweite Aspekt ist, dass bei der E-Mobilität infolge des nicht vorhandenen Motorgeräuschs unangenehme Nebengeräusche störender auffallen. Um das zu vermeiden, müssen viele Bauteile – etwa Zahnräder, Gelenkwellen oder auch Fahrwerkskomponenten – deutlich engere Toleranzvorgaben erfüllen.
Welche besonderen Herausforderungen stellen Komponenten für die E-Mobilität an die Werkzeuge?
Die grundsätzlichen Werkzeuglösungen für fast alle Bearbeitungsaufgaben im Zusammenhang mit der Elektromobilität sind seit längerem bekannt. Aber es reicht nicht, sie einfach zu übernehmen. Entscheidend ist die Transferleistung von der Ursprungsanwendung in die Serienproduktion. Ein Beispiel dafür ist das Bearbeiten von Aluminiumteilen für die Luftfahrt. Dort spielen weder die kurzen Taktzeiten noch der extreme Kostendruck, die in der Autoindustrie normal sind, eine entscheidende Rolle. Mitunter reicht es, mehrere Operationen in ein Werkzeug zu integrieren. Oft ist aber auch eine andere Prozessführung oder ein neues Fertigungsverfahren nötig.
Wie gelingt es Ihnen, das zu meistern?
Es ist wichtig, den Kunden zuzuhören, zu verstehen, welche Probleme sie haben. Die Transferleistung von der Ursprungsanwendung in die E-Mobilität erfordert einiges an Engineering. Deshalb sind wir auch an einigen Forschungsprojekten beteiligt, in denen es unter anderem darum geht, Prozesse effizienter zu gestalten.
Mussten Sie für die E-Mobilität spezielle Werkzeuge entwickeln?
Gerade in der Serienfertigung muss man sehen, dass es beispielsweise verschiedene Aluminiumsorten gibt, deren unterschiedliche Legierungsbestandteile die Zerspanungseigenschaften des Materials verändern. Hier geht´s beim Auslegen eines Werkzeugs, dessen Leistungsfähigkeit oder Standzeit oft um Nuancen, die in der Summe deutliche Vorteile hinsichtlich Taktzeit und Kosten bringen. Natürlich haben wir hier – je nach Anforderung des Kunden – gezielt optimierte Lösungen entwickelt, die in der jeweiligen Situation das bestmögliche Ergebnis liefern.
Welchen Anteil hat die E-Mobilität in Ihrem Unternehmen heute?
Nicht den, den wir aufgrund politischer Vorgaben und vieler medialer Berichte erwarten würden. Die Automobilindustrie hat durch unsere breite Aufstellung in unterschiedlichsten Zielbranchen nicht mehr die dominierende Rolle bei Horn, wenngleich sie weiterhin eine unserer wichtigsten Kundenbranchen ist. Aber die E-Mobilität hat bei uns auch deshalb eine vergleichsweise untergeordnetere Bedeutung, weil der Verbrenner nach wie vor einen hohen Stellenwert hat. Daran, dass infolge der kurzfristigen Streichung staatlicher Subventionen rund 100.000 E-Fahrzeuge weniger bestellt wurden als zuvor, sieht man, dass die E-Mobilität nicht die durchdringende Bedeutung hat, die mancher ihr gerne beimessen will. Unabhängig davon ist sie zumindest ein Teil der Zukunft und bietet auch interessante Bearbeitungen. Gerade aufgrund der höheren Präzisionsanforderungen kommen wir jetzt an Bauteile heran, die uns zuvor verschlossen geblieben sind.
Welche weitere Entwicklung erwarten Sie bei den Antriebskonzepten?
Die Chinesen waren uns in Sachen E-Mobilität einen gewissen Zeithorizont voraus. Nach dem Wegfall der staatlichen Subventionen gingen dort aber bei vielen kleineren Betrieben die Lichter aus, und es kam zu einer Marktkonsolidierung. Inzwischen ist zu beobachten, dass die verbliebenen Hersteller ihre Exporthäfen ausbauen. China ist also gerade in Phase 2 – nach dem Aufbau der Technologie folgt jetzt das Streben in die Welt. Wir in Deutschland haben diese Entwicklung anfangs etwas verschlafen und uns andererseits politisch unsere Stärke – den Verbrennungsmotor – nehmen lassen. Jetzt bewegt sich die Verbrennertechnik – in der Welt noch immer ein valides Antriebskonzept – aus Deutschland heraus. Gleichzeitig drängen E-Mobilitätsanbieter aus China oder den USA auf den deutschen Markt. Das ist ein hochgefährlicher Trend, weil wir jetzt in keiner Antriebsvariante mehr führend sind. Zudem sehen wir, dass die hier hergestellte Produktionstechnik überwiegend in den Export geht, und unsere Fahrzeughersteller erleben bereits eine Senke in der Nachfrage und der Produktion. Aus meiner Sicht haben wir unsere führende Position vorerst verloren.
Welche Konsequenzen wird das haben?
Nachdem der Verbrennungsmotor in Deutschland und Europa nicht mehr gewünscht ist, müssen wir uns überlegen, wo der Strom für eine umfassende Elektromobilität herkommen soll. Die dazu notwendige Infrastruktur rechtzeitig aufzubauen, wäre Sache der Politik gewesen und wurde bislang nicht ausreichend umgesetzt. Auch deshalb müssen wir erkennen, dass der Wunsch, in der EU bis 2030 reinelektrisch zu fahren, utopisch ist. Hier müssen sich Politik und Gesellschaft der Realität stellen. Wenn wir in irgendeiner Art und Weise in die Zukunft fortschreiten und nicht technologisch stehenbleiben wollen, dann brauchen wir – neben dem Bekenntnis zur E-Mobilität – auch andere Antriebskonzepte und ein Bekenntnis zum modernen Verbrennungsmotor – spritsparender als heute, mit CO2-neutralen Kraftstoffen, hybrid unterstützt. Hier gäbe es einige Möglichkeiten, die technisch durchaus machbar und sinnvoll wären, aber politisch leider abgewürgt werden.
Was bedeuten die bisherigen Vorgaben für unsere künftige Mobilität?
Bei der E-Mobilität kommt nur derjenige kostengünstig zum Strom, der auf seinem Dach eine PV-Anlage hat und sein Auto tagsüber zuhause parken und laden kann. Für alle anderen ist das Laden eines E-Fahrzeugs ähnlich teuer wie das Tanken an der Tankstelle. Das Wunschdenken der Politik und gewisser Lobbyisten geht komplett an der Realität vorbei. E-Mobilität bietet nur dann eine Chance, umweltfreundlicher zu sein, wenn man regenerativ erzeugten Strom tankt. Aber: Wer grünen Strom kauft, bekommt diesen nur zu einem Bruchteil. Das ist moderner Ablasshandel. Mir wäre lieber, wir könnten endlich konstruktiv an Lösungen arbeiten, anstatt diese Einstellung – wir verbieten das, und die Menschen werden schon klarkommen – weiterzutreiben.
Welche Konsequenzen erwarten Sie daraus resultierend für Ihre Branche?
Die Veränderung der Veränderung ist ja unser Lieblingsthema. Wir werden weiterhin neue Verfahren entwickeln – das Wälzschälen ist ein Beispiel aus der Vergangenheit –, wir werden neue Beschichtungen und Substrate entwickeln und sie an veränderte Anforderungen anpassen, die sich aufgrund des sich entwickelnden Marktes ergeben. Das Schöne ist: Das ist schon immer unsere Firmenphilosophie. Wir müssen also unsere Instinkte nicht verändern, wir können unsere Technik kontinuierlich weiterentwickeln. Die Ergebnisse werden unter anderem im September in Stuttgart auf der Fachmesse AMB zu sehen sein. Dort präsentieren wir neue Technologien, Prozesse und innovative Werkzeuglösungen.
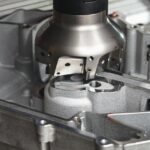
Bild: Paul Horn/Sauermann
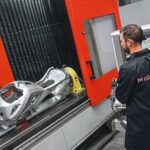
Bild: Paul Horn/Sauermann
Diese Motorrad-Komponenten stellen höchste Anforderungen
Vor rund 30 Jahren begann der Franzose Olivier Midy, sein Traummotorrad zu entwickeln. Kennzeichen der Midual Type 1 sind zahlreiche technische Spezialitäten. So hat das 165.000 Euro teure Motorrad statt eines Rohrrahmens ein Aluminium-Sandguss-Monocoque, das viele Funktionen integriert, sowie einen längs und geneigt eingebauten Zweizylinder-Boxermotor. Maschinenbauingenieur Midy wollte mit seinem Konzept und technischer Perfektion alles bislang Dagewesene in den Schatten stellen. Zu seiner Philosophie gehört eine möglichst hohe Fertigungstiefe. Für die CNC-Bearbeitung stehen in seiner Produktion zwei CNC-Fräszentren.
Zu den Frästeilen zählen neben Motorkomponenten und Rahmen auch Halterungen, Fußrasten sowie weitere Anbauteile. Die meisten Kleinteile der Type 1 sind aus dem Vollen gefräst. Kunststoffteile findet man an diesem Motorrad so gut wie keine. Für zahlreiche Fräsoperationen setzt Midy auf Werkzeuge von Paul Horn.
Zum Planfräsen des zweiteiligen Motorgehäuses aus einer Aluminiumlegierung suchte Midy nach einer passenden Bearbeitungslösung, die seine hohen Qualitätsanforderungen erfüllt. Weil die Fräsflächen zugleich als Dichtflächen dienen, müssen sie enge Toleranzvorgaben einhalten. Neben der Ebenheit ist auch eine hohe Oberflächengüte wichtig.
PKD erzeugt hochglänzende Oberflächen
Zum Einsatz kommt hier das Frässystem DTM von Horn mit einem Durchmesser von 80 mm und Schneiden aus polykristallinem Diamant (PKD). Die guten Gleiteigenschaften der Diamantoberfläche beugen in Kombination mit der internen Kühlmittelzufuhr der Bildung von Aufbauschneiden vor.
Kommen fürs Fräsen hochglänzender Oberflächen normalerweise Schneiden aus monokristallinem Diamant zum Einsatz, so lassen sich mit den qualitativ hochwertigen PKD-Schneiden und einem perfekten Prozess ebenfalls extrem gute Oberflächen bis hin zum Spiegelglanz erzeugen.
Neben der Qualität der Schneideinsätze spielt das Haltersystem eine entscheidende Rolle. Die Plattensitze des Trägerwerkzeugs sind mit einem Justiersystem ausgestattet. Der Planlauf lässt sich mithilfe eines Voreinstellgeräts µm-genau justieren. Die geringe Masse der aus Aluminium gefertigten Trägerwerkzeuge reduziert den Energieaufwand und ermöglicht hochdynamische Fräsprozesse. Um dem Verschleiß am Grundkörper vorzubeugen, ist er mit einer Hardcoat-Beschichtung versehen.
Schrauben aus dem Vollen gefräst
Jedes einzelne Bauteil der Type 1 muss hohen Qualitätsansprüchen genügen und ist möglichst aus dem Vollen gefräst. Midy fertigt sogar die Schrauben, die die Lederapplikationen halten, selbst. Da er noch keine CNC-Drehmaschine besitzt, sind die Schrauben gefräst und mit dem Midual-Logo graviert. Dabei setzt er unter anderem aufs Zirkular-Frässystem von Horn, das – neben dem Nut- und Zirkularfräsen – auch beim Trennfräsen eine hohe Leistung bringt.
Fürs Stoßen der Steckverzahnungen – etwa im Schalthebel – setzt Midy auf das Horn-Werkzeugsystem Supermini des Typs N105. Die präzisionsgeschliffene Werkzeugschneide gleicht hierbei dem Profil der Verzahnung. Ist ein Zahn fertig, dreht die Spindel weiter, um den nächsten herzustellen. (mw)
Weitere Infos: https://hier.pro/zQHF8
Hier finden Sie mehr über: